Foam Sandwich construction - Part 1
Foam Sandwich for amateurs - Part one: Overview
How to build a foam sandwich composite boat
These notes will describe step by step how to build a boat in foam sandwich composite.
The notes below are not about comparing materials, we focus exclusively on building.
Appropriate foams for the methods we describe below are Divinycell, Klegecell, CoreCell and Airex (2007). We will only use epoxy as resin: no polyester or vinylester.
Epoxies formulated for wooden boat building are not always adequate for foam sandwich.
Ideally, the builder should use a two phase resin. This means a resin that requires a post cure at a higher temperature. Consult your designer about the correct type of epoxy.
Foam sandwich is a well proven material, light and strong. It is particularly well adapted to the building of one-off hulls. It is well suited to amateur boat building because it does not require a female mold or any special equipment.
We will describe what is commonly called the open mold method. Once you master the open mold technique, you can graduate to vacuum bagged or infused hulls.
We will focus on the techniques specific to foam sandwich. Please refer to general boat building books for details about building steps common to all methods such as strongbacks set up, bulkheads alignment, outfitting, etc.
Most books about boat building describe the techniques we use in great detail. We recommend "The Gougeon Brothers on Boat Construction".
The techniques we show are common to all hull types, power or sail.
Overview of the hull building method:
We will create a foam hull shape around a wooden jig, fiberglass the outside, flip the hull, remove the jig and fiberglass the inside skin. After completion of the hull, the internal components will be added. The deck will be built the same way as the hull.
Those familiar with our plywood epoxy (stitch and glue composite) method will recognize the procedure.
The differences in building methods between plywood composite and foam sandwich result from the difference in stiffness between the two materials. Plywood is stiff and will require less molds. In plywood cored composite, the frames and bulkheads can often be used as molds. In favor of the foam is the ease of cutting and the flexibility: no need to fight the core material while bending the panels or planks.
Foam is more flimsy and must be supported by a more dense structure. We will use either closely spaced molds or battens on molds or a combination of the two.
A major difference is the lamination schedule. The fiberglass skins used in foam sandwich are much thicker than in plywood sandwich.
Building a foam sandwich boat step by step:
• build a jig
• plank the jig with foam panels
• fiberglass the outside
• flip the hull
• remove jig
• fiberglass inside
• install internal structure
• install systems: machinery, tanks, electrical
• build superstructure
In pictures, hull only:
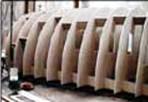
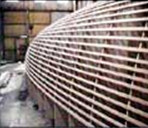
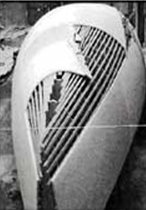
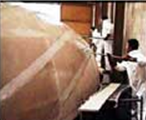
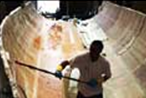
1: molds 2: optional slats 3: cover with foam 4: fiberglass out 5: glass in
This file will focus on the building of the hull, deck and structural elements. For the accommodations, systems installation and paint please see our on line tutorials or refer to specialized books and supplier's technical documentation.
Materials and jig types:
The specifications for the jig such as the number and spacing of molds and the use of battens depends on the type of core materials: foam sheets or foam strips.
Wide foam sheet planking:
The foam can be used in large sheets (the size of a plywood sheet). In that case, we will often use scored foam (= contoured foam). Boats with hull panels close to developable surfaces can use plain sheets of foam.
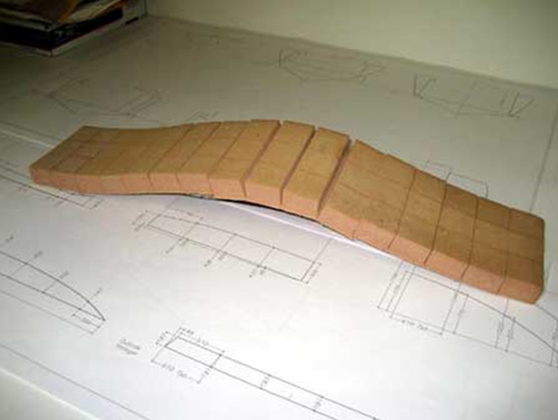
Scored or contoured foam is foam with deep cuts on one or the two sides. It conforms easily to almost any shape.
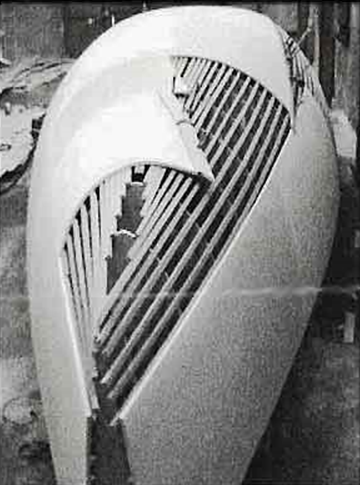
The very flimsy sheets of scored foam require more support than just the molds. We use battens (slats) over the molds to support the sheet and shape the foam accurately.
In most cases, battens spaced 6" between centers will suffice. Before installing the foam over the battened molds (sometimes called a slat mold), some builders cover the whole assembly with a sheet of plastic to prevent the resin from leaking through gaps and bonding to the jig.
The foam sheets are usually fastened to the mold by nails or screws.
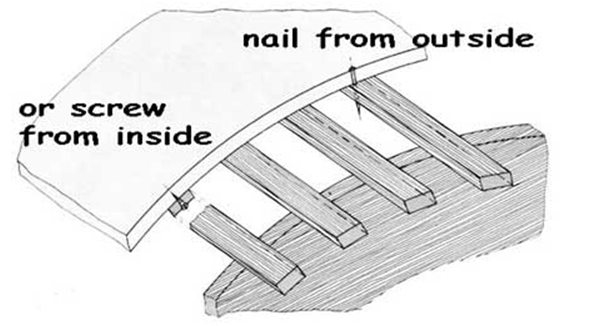
Those fasteners are removed after the hull is turned over. Headless nails can be pulled through the battens from inside.
In some cases, nails with buttons are required. Buttons are small pieces of plywood acting as a washer.
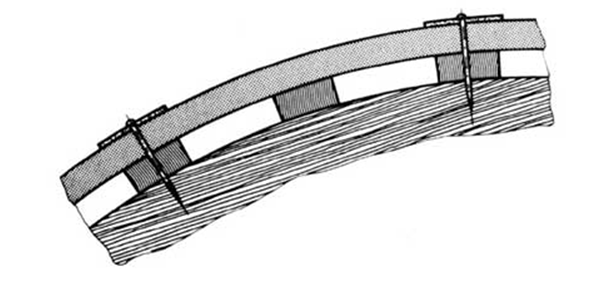
The slat mold method is the most common in professional boat building. A good slat mold can be used many times.
It is more labor intensive than strip planking methods not only because of the slats but to apply the large panels requires two men.
For amateur boat building, the foam strip planking is faster and easier.